Home / Parts and Shapes
Delrin® can be extruded into rods, bars and sheets ready for machining.
Customize, tailor and tweak Delrin-machined parts to get exactly what you want. Bridging the gap between plastics and metals for a wide range of technical applications.
Prototype and make small production runs with confidence! Delrin offers the opportunity to machine parts that will have close performance to a molded component. Whether for commercial applications or to assess the performance of a new idea, designers and engineers can benefit from the ease of machining with Delrin and the unique properties it brings to the final parts.
Not all acetals are equal – “ask for Delrin®”
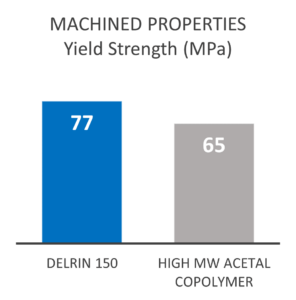
Parts machined from Delrin deliver superior strength, stiffness, and toughness – its is also widely chosen for repeat loaded applications, outperforming alternative materials such as acetal copolymer.
Thanks to the high crystallinity of Delrin, this advantage is maintained across a wide range of temperatures, making it the ideal material for a variety of machined products including valve components, gears, bearings, rollers, fittings, bushings and spacers, to name a few.
When you need to machine parts for demanding applications. It pays to “ask for Delrin.”
Discover the ease of machining Delrin®
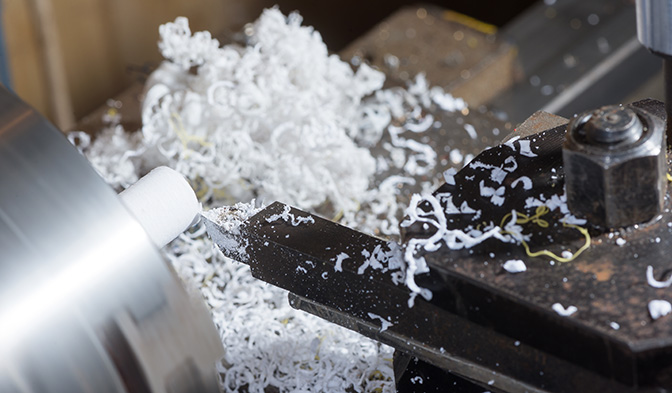
Delrin is a stable material and cuts very well, which makes precise, tight tolerances easier to achieve.
To get the best results:
- Design for Delrin. Keep an even wall thickness and include fillet radii, especially if your prototype part will be molded in production.
- Keep cool. While machining, remember that Delrin is sensitive to heat at or above 250°F (121°C).
- Stay sharp. Maintain a sharp cutting edge. Use of cutting lubricant will help maintain a precision cutting edge.
- Clamp lightly. While Delrin is stiff it’s still a plastic; light clamping will avoid surface damage.
Discover more about machining Delrin in the Plastic Design Guide.
Performance you can rely on
When machining parts with Delrin, all key properties are maintained – giving greater confidence when transitioning to moulded parts. This is unlike machining glass filled resins given the way that the fibres align, which is very different to a molded part.
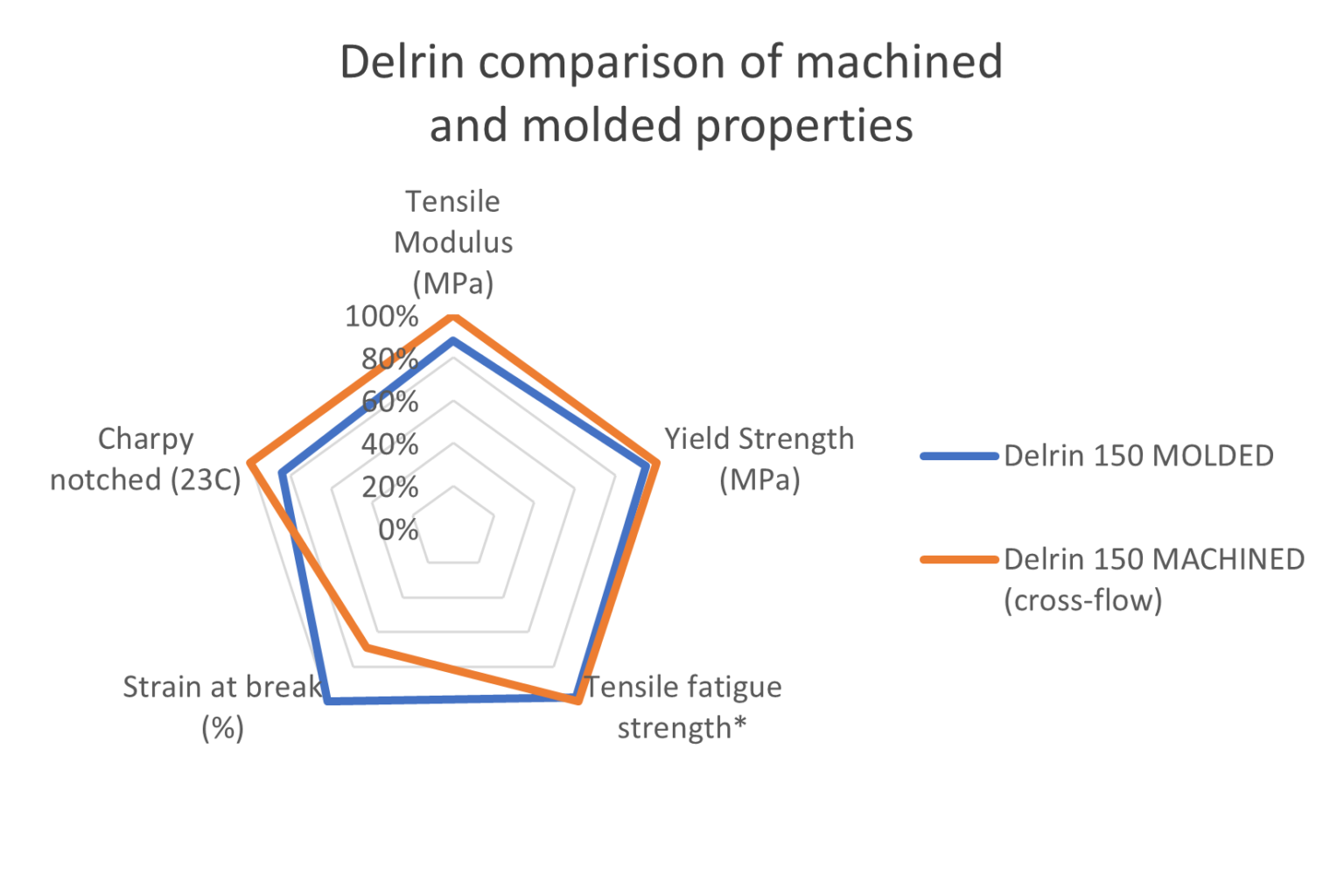
*At 1 million cycles
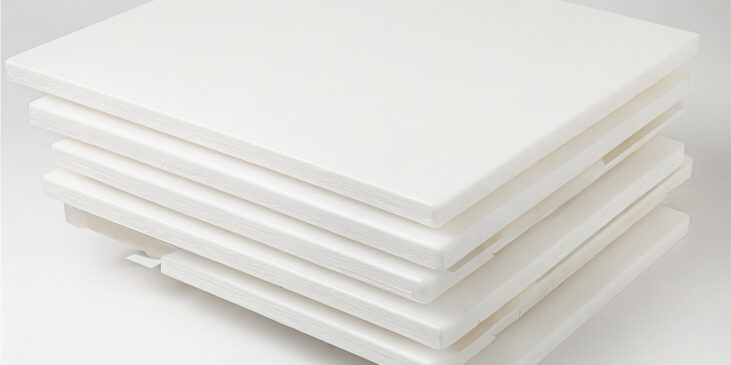
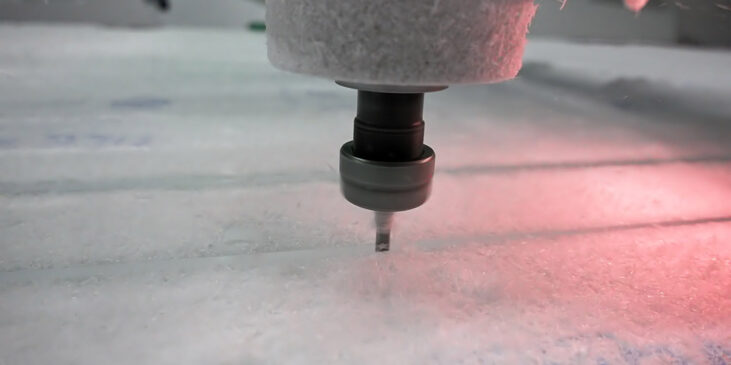
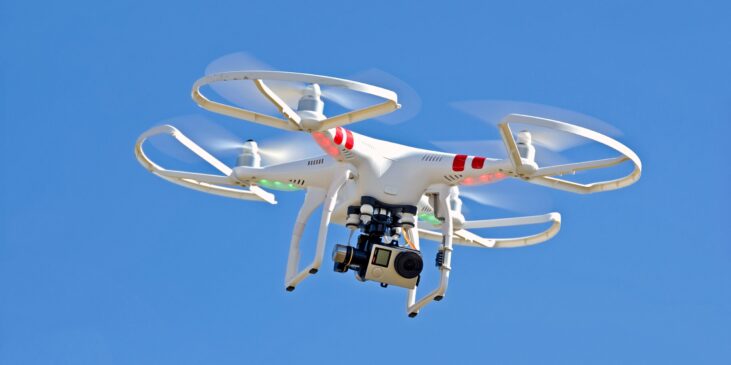