デルリンギアを精密に成形
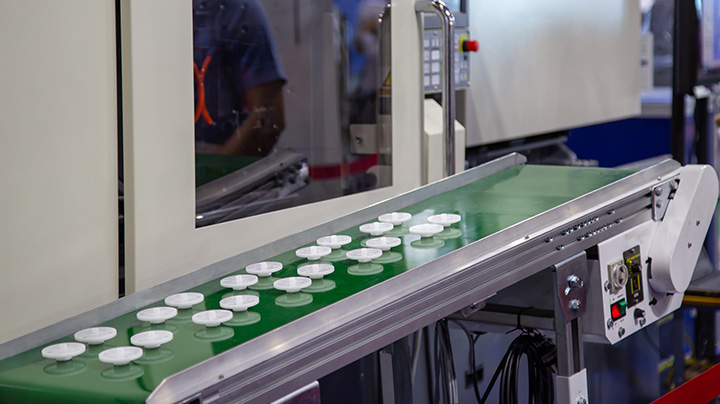
ギアを成形する際に考慮しなければならないのは、寸法精度と真円度である。
ほとんどの歯車用途では、非強化グレードのDelrin®が使用されており、ガラス強化材料よりも流れ方向に対して収縮が均一であるため、大きな利点があります。一方、ガラス繊維強化材は、ガラス繊維に垂直な方向の収縮率が高く、流れ方向の収縮率は低くなります。この不均一な収縮は、部品の歪み(反り)や真円度の損失をもたらす可能性がある。
とはいえ、Delrin®でギアを成形する場合、寸法安定性を最適化するために考慮しなければならない重要な要素があります:
- ゲートの位置と充填パターン
- 収縮に影響する設計上の特徴
- 溶融物から固形物への収縮を補うため、より多くの材料を投入することによる部分充填
ゲート位置
プラスチックが工具の空洞に充填される方法は、可能な限り均等に充填されるように研究されるべきである。
理想的なケースでは、プラスチックはギアの両端を同時に満たすので、円形ギアではセンターゲートが最良の選択肢であることを示唆しているが、考慮すべきことは他にもある。
収縮に影響する設計上の特徴
また、部品の充填パターンを調べることで、設計上の特徴が部品の収縮に影響するかどうかの目安を得ることができる。
これらの例では、軽量化のために部品に切り欠きがある。
システム効率を向上させるためには歯車の軽量化が望ましいが、この場合、設計変更によって穴の周囲に異なるレベルの収縮が発生し、歯部の真円度が低下した。
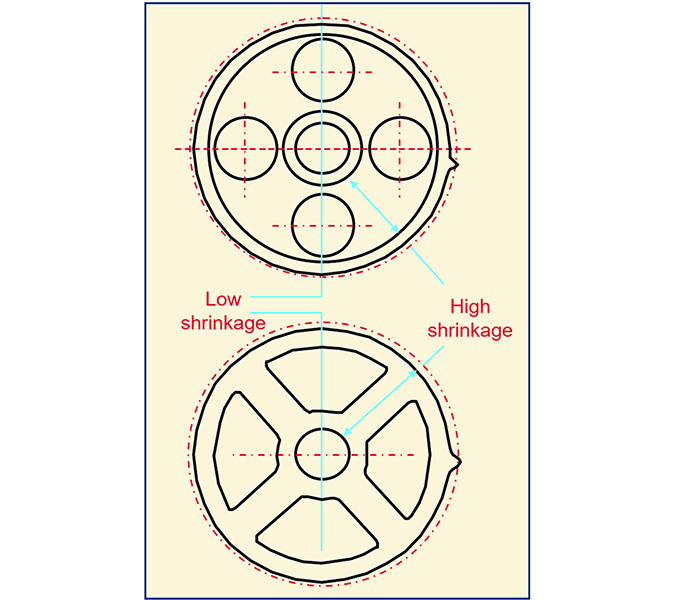
同じような効果は、流動に影響を与える他の設計上の特徴、例えば、流動にためらいを生じさせる薄いリブや、次のポイントにつながるが、よく詰まったとしても全体的に収縮率の高い厚い部分などでも観察される。
部品梱包
パッキングは、溶融から固体のDelrin®への収縮を補うために、より多くの材料をキャビティに注入する加工段階です。
Delrin®コンポーネントの性能と寸法安定性には、射出成形工程で完全に充填することが重要です。そうでない場合、収縮率が高くなり、ギアの強度を低下させるボイドが発生する危険性があります。
ギアが完全に充填されるようにするには、早期凍結しないゲート・ランナー方式で最も厚い部分に注入する必要がある。
これを図にすると以下のようになる:
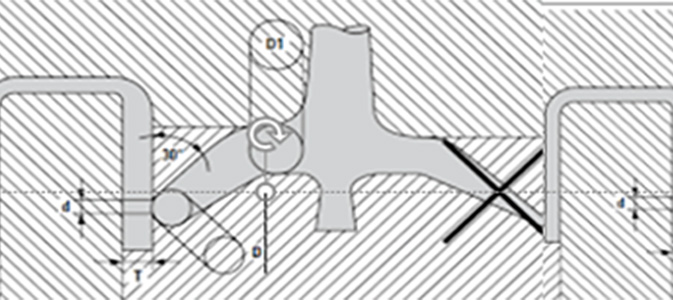
右側では、ゲートがテーパーをつけすぎて、最も薄い部分に供給されている。
この部分のプラスチック材料が先に固化し、厚い部分の中央の材料はまだ溶けている。
これ以上材料が送り込まれないため、収縮が激しくなり、表面が陥没したり、中心部にボイドが生じたりする。
左の設計では、部品を完全に充填し、制御できない収縮を避けるために、より多くの材料をより長く厚い部分に供給することができます。
ゲートの直径 "d "は、部品の厚さ "T "の半分以上でなければなりません。
ゲートの長さは0.8mmより短くする。
ゲートに隣接するランナーの直径 "D "は、部品厚さ "T "+1mm以上でなければならない。
「D1 "は "D "よりも大きくなければならない。 詳しくはデルリン成型ガイドをご覧ください。
最適なサイクルタイムでギアを成形するために、均一な肉厚を維持するためのアイデアを以下に示します。
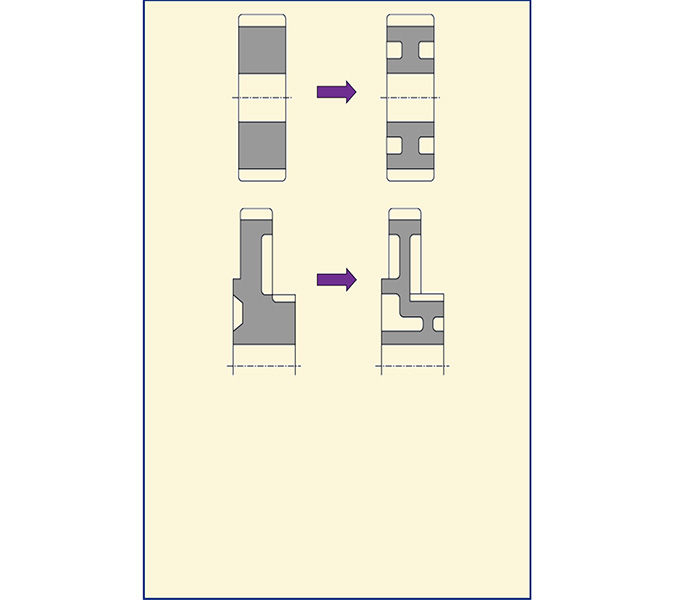
Moldflow®のような充填シミュレーションソフトウェアを使用すると、射出成形金型を作成する前に、成形サイクル、パッキング、部品の収縮をすべて調査することができます。
これは、ギア部品を最適化するために正しい決定が行われていることを確認するために推奨されます。
Delrin®の多くのグレードは、このようなシミュレーションソフトウェアで使用するために完全に特性化されています。