Mouler des engrenages en Delrin® avec précision
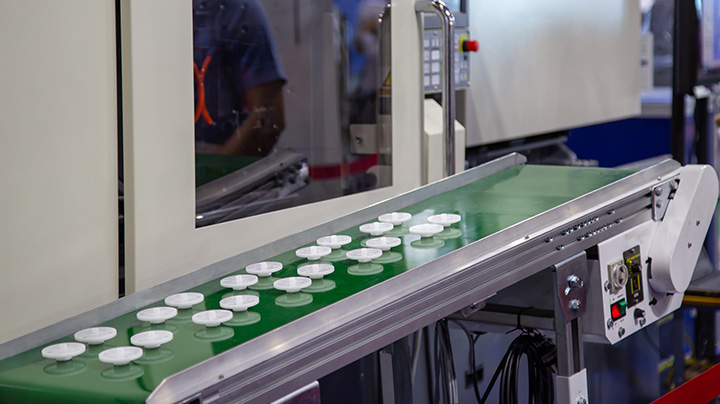
L'une des principales considérations pour le moulage d'un engrenage est la précision dimensionnelle et la circularité.
Dans la plupart des applications d'engrenages, on utilise des grades non renforcés de Delrin®, ce qui présente un grand avantage par rapport à un matériau renforcé de fibres de verre, car le retrait est plus régulier par rapport à la direction de l'écoulement. Les matériaux renforcés de fibres de verre, en revanche, présentent un retrait élevé perpendiculairement à la fibre de verre et faible dans le sens de l'écoulement. Ce retrait inégal peut entraîner une déformation de la pièce (gauchissement) et une perte de circularité.
Cela étant, il reste des facteurs importants à prendre en compte pour optimiser la stabilité dimensionnelle lors du moulage d'engrenages en Delrin®:
- Emplacement du point d’injection et mode de remplissage
- Caractéristiques de conception qui influencent le retrait
- Pression et temps de maintien pour s’assurer du remplissage de l’empreinte en compensant la différence de volume entre la matière fondue et solide.
Emplacement du point d’injection
La façon dont la matière remplit toutes la cavité de l'outil doit être étudiée afin d'assurer un remplissage aussi uniforme que possible.
Dans un cas idéal, la matière remplit toutes les extrémités de l'engrenage en même temps. Avec un engrenage circulaire, cela suggère qu’un point d’injection central serait la meilleure option, mais il y a d'autres éléments à prendre en considération.
Caractéristiques de conception qui influencent le retrait
L'étude du schéma de remplissage de la pièce permet également de savoir si l'une des caractéristiques de la conception aura un impact sur le retrait de la pièce.
Dans ces exemples, des découpes ont été pratiquées dans la pièce pour gagner du poids.
Bien qu'il soit souhaitable d'alléger les engrenages pour améliorer l'efficacité du système, dans ce cas, la modification de la conception a entraîné différents niveaux de retrait autour des découpes , ce qui a contribué à un défaut d'arrondi au niveau des dents.
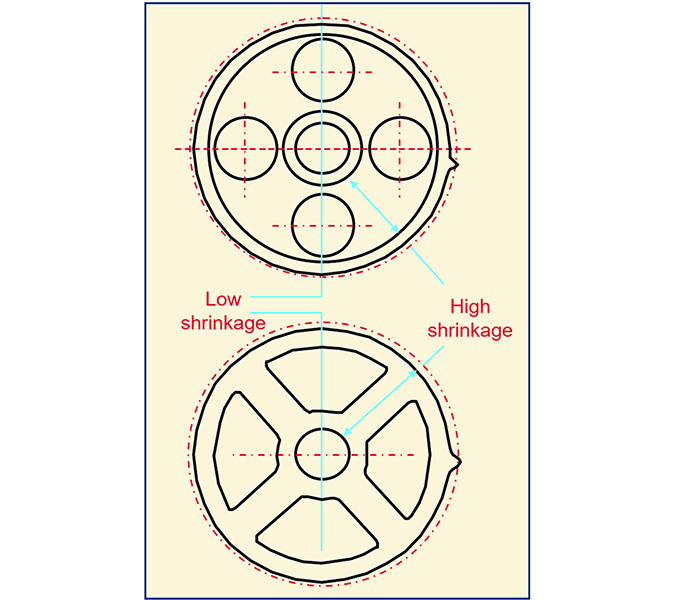
Un effet similaire pourrait être observé avec d'autres caractéristiques de conception qui affectent l'écoulement, telles qu'une nervure fine qui crée une restriction d’écoulement ou une section épaisse qui a un retrait global plus élevé, même si le maintien est suffisant, ce qui nous amène au point suivant.
Pression et temps de Maintien
Le maintien est la phase de mise en œuvre où l'on injecte plus de matière dans la cavité pour compenser la différence de volume entre Delrin® à l'état fondu et à l'état solide.
Il est essentiel pour les performances et la stabilité dimensionnelle d'un composant en Delrin® qu'il soit entièrement rempli pendant le processus de moulage par injection. Si ce n'est pas le cas, il y aura un risque de présence de vides qui pourraient réduire la résistance de l'engrenage.
Pour s’assurer du bon remplissage, il faut que l’injection se fasse dans la section la plus épaisse de la pièce et que le système de canaux et point d’injection ne gèle pas prématurément.
Cette situation est illustrée ci-dessous :
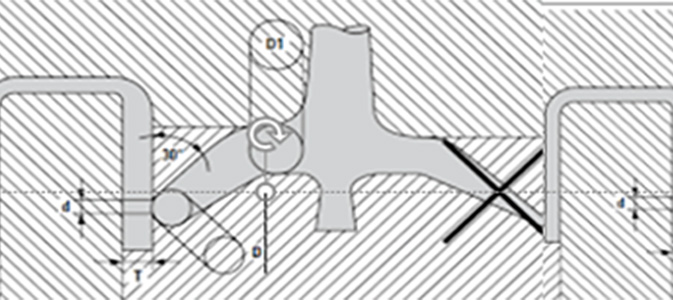
À droite, le canal se rétrécit trop et la matière est introduite dans la section la plus fine.
La matière se solidifie dans cette zone en premier, tandis qu’au centre de la section épaisse elle est toujours fondue. La pièce n'étant plus alimentée en matière, il y aura un niveau élevé de retrait, ce qui entraînera un affaissement de la surface ou des vides au centre.
La conception de gauche permet d'introduire plus de matière dans la section épaisse pendant plus longtemps afin de remplir complètement la pièce et d'éviter un retrait incontrôlé.
Le diamètre du point d’injection "d" doit être au moins égal à la moitié de l'épaisseur de la pièce, "T".
La longueur du point d’injection doit être inférieure à 0,8 mm.
Le diamètre "D" du canal à côté du point d’injection doit être au moins égal à l'épaisseur de la pièce "T "+1mm.
"D1" doit être plus grand que "D". Vous trouverez de plus amples informations dans le guide du moulage du Delrin.
Vous trouverez ci-dessous quelques idées pour maintenir une épaisseur de paroi régulière, ce qui permettra de mouler un engrenage avec un temps de cycle optimal.
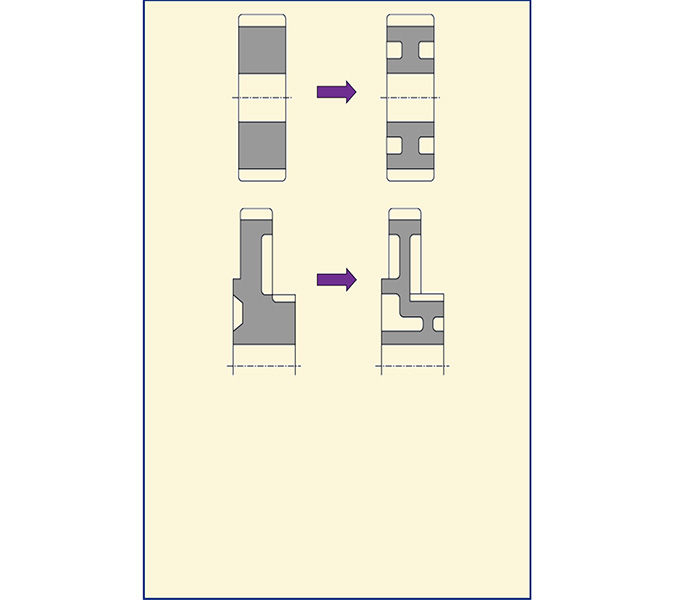
L'utilisation d'un logiciel de simulation de remplissage, tel que Moldflow®, permet d'étudier le cycle de moulage, le maintien et le retrait de la pièce avant la fabrication du moule. Cette démarche est encouragée pour s'assurer que les bonnes décisions sont prises afin d'optimiser la pièce d'engrenage.
De nombreux grades de Delrin® sont qualifié pour être utilisés dans de tels logiciels de simulation.