Consigue la ventaja del diseño Delrin
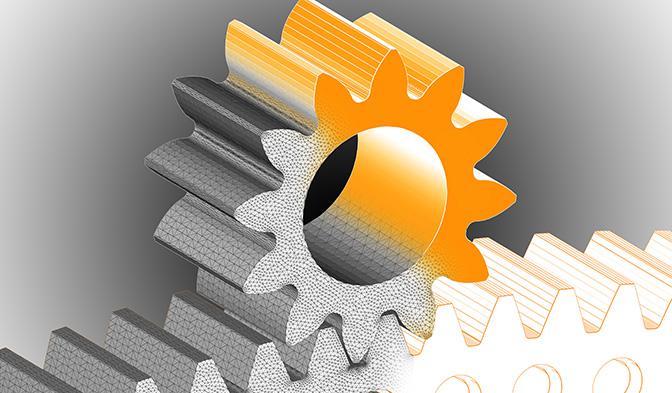
Obtén soluciones incluso para los retos de engranajes más difíciles recurriendo a los expertos de Delrin® para el Análisis de Elementos Finitos (AEF).
El equipo de diseño de Delrin® está preparado para colaborar contigo en el diseño del engranaje óptimo.
Desde el cálculo manual hasta el AEF avanzado, sabemos cómo predecir con precisión el comportamiento del material Delrin® para ayudarte a diseñar mejores engranajes de plástico.
Software de diseño de engranajes
Para el trabajo de simulación, Delrin® utiliza un software comercial de diseño de engranajes ampliamente utilizado en la industria para apoyar el diseño de engranajes de plástico e incorpora las normas VDI (2736) más relevantes en el cálculo del software.
Para los engranajes de plástico, puede predecir:
- Modos de fallo
- Cálculo del desgaste
- Análisis de contactos
- Cálculo del juego de funcionamiento
Se han caracterizado varios grados de Delrin® específicamente para este tipo de software de diseño de engranajes, con el fin de incluir datos generales del material, fatiga de la raíz y factores de desgaste.
La mejor forma de utilizar el software es como herramienta de cribado para reducir al mínimo las pruebas reales de material que hay que realizar.
Técnicas de análisis por elementos finitos (AEF) aplicadas a los engranajes
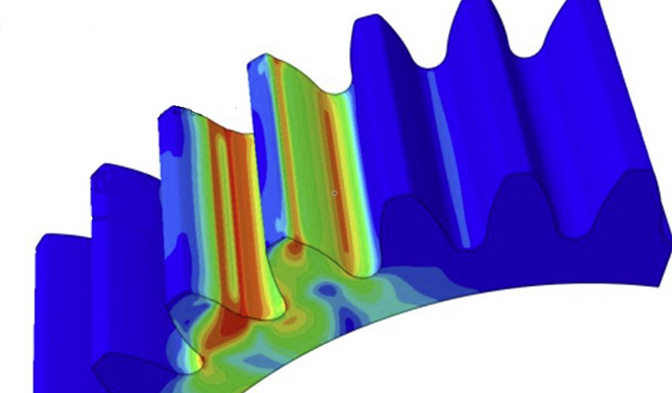
El avanzado equipo de ingeniería asistida por ordenador (CAE) de Delrin® proporciona capacidades de primera clase para ayudar a los clientes en el desarrollo de sus productos.
Un ejemplo es el diseño por AEF de engranajes de plástico, que ofrece una simulación realista de la vida útil, la durabilidad y el reparto de cargas de los engranajes de plástico.
Es capaz de captar el daño progresivo, la plasticidad y los mecanismos de deformación cíclica, y proporcionará información valiosa durante el proceso de diseño.
En el ejemplo de la Figura 1, se modeló un conjunto de engranajes de 40 dientes y 0,8 módulos, siendo idénticos el engranaje motor y el engranaje conducido.
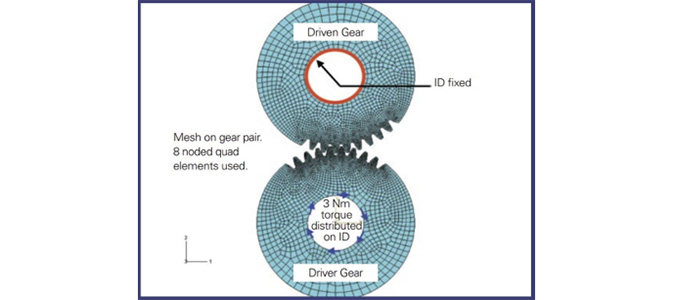
En las pruebas reales de vida a fatiga de los engranajes, éstos funcionaban a 100 rpm con un par de 3 N-m, y el fallo se producía normalmente en unos 10 minutos.
Los mismos engranajes fueron modelados por los ingenieros de Delrin® mediante un programa de elementos finitos, como se muestra.
El engranaje conducido estaba fijo en su diámetro interior, mientras que el conducido tenía un par de 3 N-m distribuido uniformemente en su diámetro interior.
El material para esta prueba fue Delrin® 100P.
En un análisis de elementos finitos no lineal, la carga se aplica en incrementos hasta alcanzar la carga máxima.
La figura 2 muestra algunos de los incrementos.
En cada incremento sucesivo, las tensiones de Von Mises son mayores y se extienden a más dientes a medida que éstos entran en contacto.
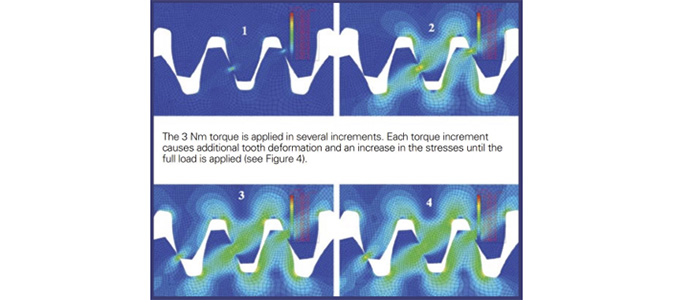
La figura 3 muestra las tensiones de Von Mises en los engranajes de prueba a la carga máxima, 3 N-m.
Esta figura muestra que tres juegos de dientes están en contacto simultáneamente al par máximo, por lo que se produce un cierto reparto de la carga.
Sin embargo, en algunos puntos se supera el límite elástico.
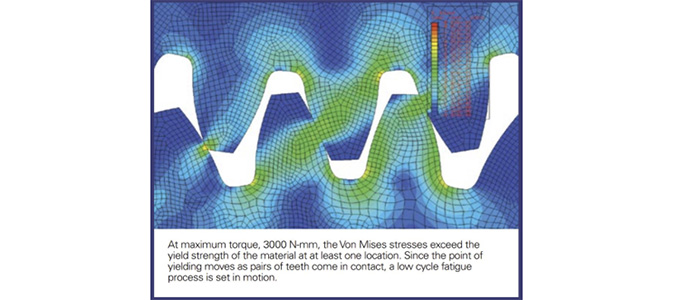
En este caso, cuando las tensiones repetidas superan el límite elástico, se produce la fatiga de bajo ciclo.
Esto significa que el fallo se produce después de relativamente pocos ciclos.
Este ejemplo demuestra que el software predice con exactitud el modo de fallo con un número de ciclos relativamente bajo, como se ha validado en las pruebas.
Cada caso es diferente, pero mediante la ejecución de estas simulaciones, los ingenieros de Delrin® pueden ayudar a poner de relieve los posibles problemas y ayudarte a optimizar los diseños de los engranajes para prolongar su vida útil.