Discover why Delrin® is chosen for gears more than other plastics

Delrin®—a widely used engineering plastic for gears—provides strength and stiffness without the need for glass fiber reinforcement. It’s the popular material of choice because it offers a superior combination of excellent mechanical properties, good lubricity, and resistance to wear, moisture, and chemicals.
Compared with Nylon PA6 or PA66, Delrin® does not absorb water making it stiffer and more dimensionally stable. And while PBT is closer in terms of stiffness, Delrin® has superior toughness which is a key property in a gear.
Here is a deeper dive into seven properties that make Delrin® ideal for gears.
1. Tensile modulus and strength
Delrin® outperforms other polymer materials and is the stiffest and strongest unreinforced engineering plastic generally available. Gears made with Delrin® have greater resistance to deformation and will transmit power more efficiently than alternative plastics, delivering higher performance and longer lifetimes.
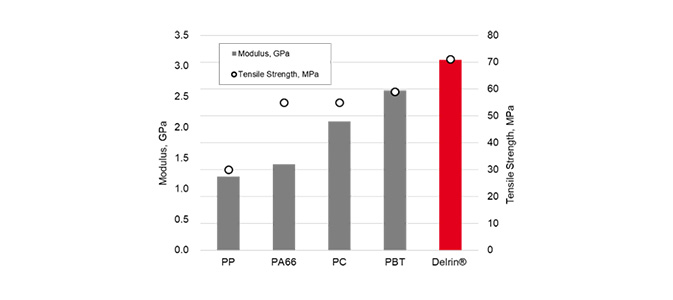
2. Fatigue
One of the most important properties for a gear is fatigue endurance, and Delrin® is the top unreinforced plastic performer again.
The chart below, tested by DuPont, compares an unreinforced PA66 conditioned at 50% RH with Delrin® 500 in flexure and the higher maximum design stress than can be used with Delrin® is clear.
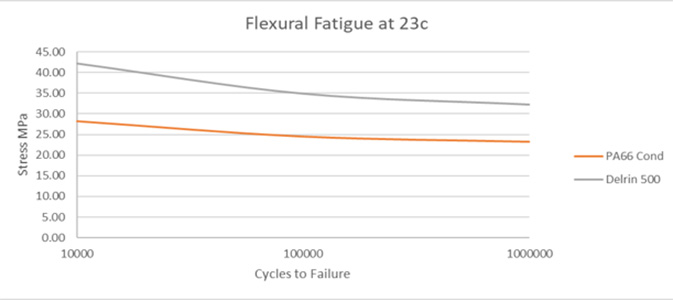
Unfortunately, only limited public data on fatigue is available. Test conditions can have a significant effect on the results which makes it difficult to compare results.
Factors that need to be considered are:
- Is the test a flexural or tension load?
- Is the load applied as positive only or fully reversed positive and negative (R number)?
- At what nominal temperature was the test run?
- What was the frequency of the test?
An additional complication is that repeated flexing generates internal heating of the part, so the speed of the fatigue test compared with the speed and time of loading of the gear needs to be considered.
Temperature increases from this testing can be in excess of 15°C, so the sample in a room temperature test can easily reach 40°C.
Delrin® is less sensitive to a temperature increase in this range compared with some other unreinforced engineering plastics.
3. Creep
Plastics are naturally more prone to creep than metals. Consequently, molded gears are best used in applications without static loads.
If static loads cannot be avoided, the creep performance of the material needs to be considered and gears designed to operate properly after the teeth have deflected due to creep.
Delrin® has excellent creep performance compared to other engineering plastics as the following chart showing creep modulus at 1000hrs at 5MPa displays
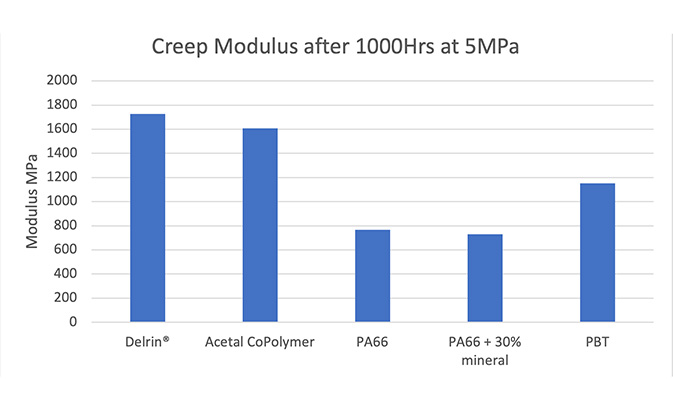
4. Dimensional stability
Being the stiffest and strongest unreinforced polymer, Delrin® can perform when other materials would require reinforcement. The most common way to reinforce a plastic is through the addition of glass fiber which is compounded into the material.
Adding glass fiber can result in two potential issues:
- The molding has uneven shrinkage in the parallel and perpendicular direction to the glass fibre, which leads to an out-of-roundness problem or a complicated compensation in the tool for the uneven shrinkage. One alternative is to use mineral reinforcement, but this is much less effective in increasing strength and stiffness.
- Faster wear occurs if the glass fibers become exposed during use. They will form a very abrasive media that can accelerate wear of the gear tooth.
Also compared with a nylon material, Delrin® offers better dimensional stability because it does not absorb moisture. Specific details on dimensional tolerance can be found in the Delrin® design guide.
5. Wear and friction
Delrin® is an inherently low friction material when compared to other polymers, which can be seen below.
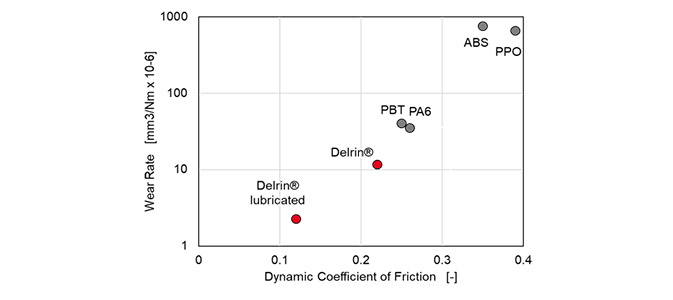
There are several advantages in adding lubricants into the polymers during production:
- Parts have longer life due to reduced wear
- Moving systems have higher efficiency due to less energy loss through friction
- Sliding surfaces can bear higher loads and run at higher velocities
- System costs can be reduced by eliminating any external lubricant
- Squeaking noise can be reduced below the audible limit
6. Chemical resistance
It is important to consider the varied environments the gear could be used in when selecting the material. For example, an amorphous material such as PC or ABS is likely to be attacked quickly by solvents.
One of the outstanding properties of Delrin® acetal resin is excellent resistance to a variety of organic and neutral inorganic compounds, even at elevated temperatures. Delrin® acetal resin exhibits good dimensional stability and superior chemical resistance to the following:
- Alcohols
- Aldehydes
- Esters
- Ethers
- Hydrocarbons (gasolines, lubricants, hydraulic fluids)
- Agricultural chemicals
- Many weak acids and weak bases
- Water
More details of the chemical compatibility of Delrin® including the mechanical properties after exposure can be found in the Delrin® Design Guide.
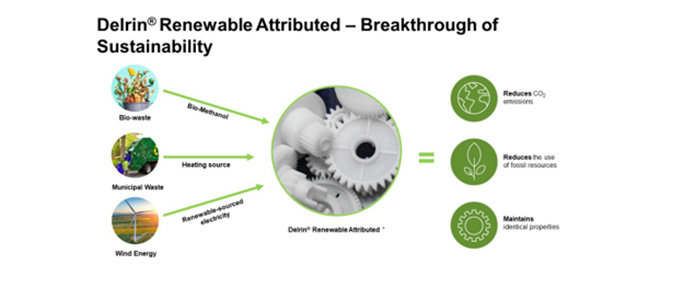
7. Sustainability
Reducing carbon footprint is becoming one the most important design objectives when developing next generation products, and Delrin® Renewable Attributed grades can help here.
Delrin® Renewable Attributed (RA) base polymer is produced from 100% bio-feedstock from waste according to ISCC Plus mass balance certification.
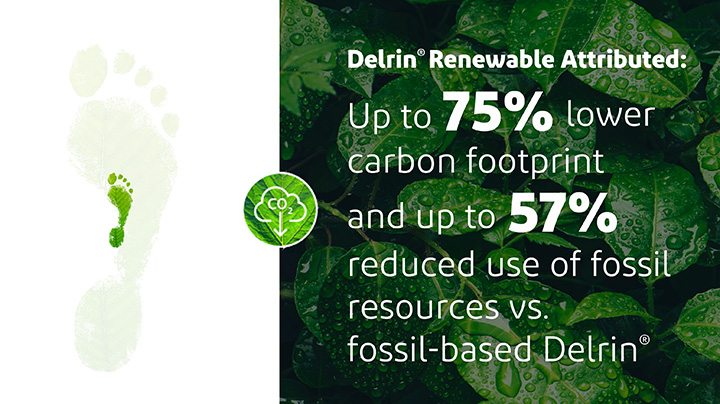
With a world-class environmental impact profile and a low carbon footprint, Delrin® Renewable Attributed offers excellent durability and reliability. It is produced from 100% certified renewable electricity, steam-sourced via municipal waste energy recovery, and offers the same quality, mechanical properties, processing, and sensory experience as Delrin®.
This makes it easy for customers to adopt Delrin® Renewable Attributed as they work toward their own sustainability goals. Continuing the Delrin® reputation, Delrin® Renewable Attributed enables lightweighting, integration of functions, and the highest levels of part performance.